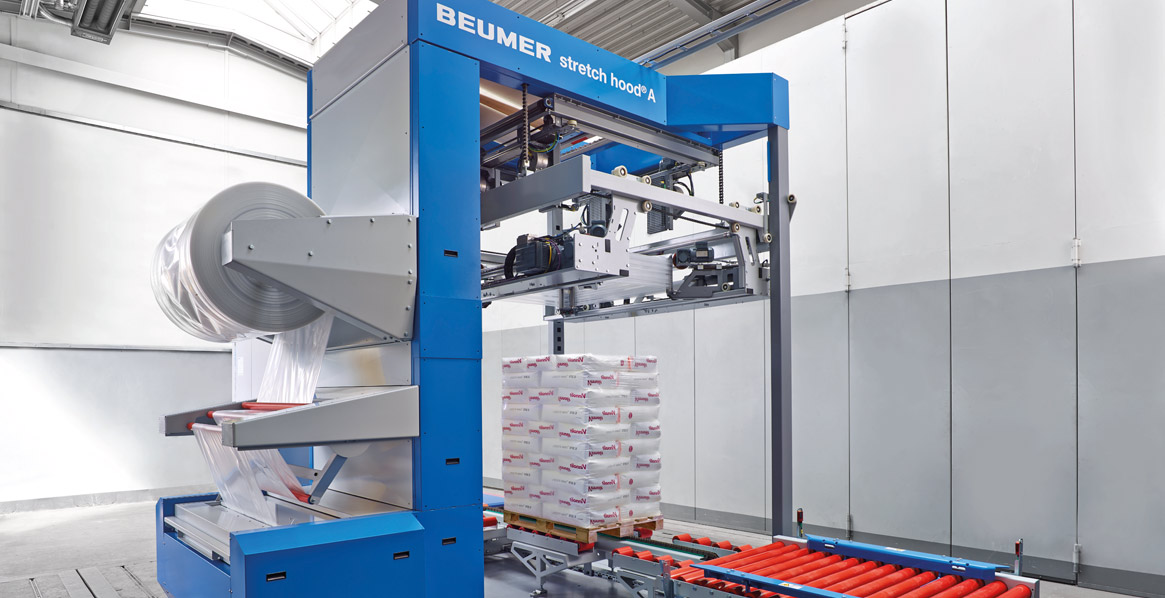
Hot Outside Passively Cooled Inside
- Product range:
- Cabinet
For operators, control cabinets - especially those used in machines and systems - mean one thing: they take up space and generate ongoing costs for cooling.
But as the example of a multi-format packaging machine from the BEUMER Group shows, both can be significantly reduced when an AirSTREAM wiring system from LÜTZE is integrated into the control cabinet. At the company’s headquarters in Beckum, Germany, three up-and-coming engineers took a deep dive into the control cabinet as part of a project. Through meticulous measurements, they recorded temperatures in two cabinets: one with a conventional mounting plate versus one with an AirSTREAM wiring frame - an electrifying comparison.
But first, a bit of background: With 5,500 employees, the BEUMER Group is a global leader in intralogistics systems - handling everything from conveying, loading, and palletizing to packaging and sorting for high-performance applications.
Passive Cooling at 35°C Outdoor Temperatures?
The project began with key questions: Shouldn’t our innovative, modular machines also feature an innovative control cabinet design? What could be achieved with a duct-free AirSTREAM system? Could we even rely on passive cooling in high ambient temperatures?
The tests were conducted on the control cabinet of a BEUMER stretch hood® machine, which wraps highly flexible film around full pallets - such as cement bags - to ensure secure transport and outdoor storage. Until now, the machine’s control cabinet has included an air conditioning unit and measured 2,000 x 1,800 mm (H x W). Thanks to a longstanding partnership, LÜTZE sales engineer Rudolf Killmann was quickly won over by the challenge. Together with Product Market Manager Bernd Hütter, he supported the project by providing a customized AirSTREAM frame and temperature sensors. Initial simulations with the online tool AirTEMP 2.0 confirmed: Yes, it’s absolutely possible.
Then came real-world testing. The most exciting result: “We were actually able to design a control cabinet where air conditioning could be eliminated up to an ambient temperature of 35°C,” reports Marc Hilgenstock, Senior Expert in Research and Development at BEUMER. In fact, by removing the air conditioning unit, the machine’s operating costs could be reduced by 24% - along with its carbon footprint. "No energy-efficient drive system in the world can achieve that kind of impact," says Hilgenstock, who supervised the three young engineers during the project.
Smaller, Lighter, More Cost-Effective
'He also confirms another key advantage of the AirSTREAM system: “Previously, the control cabinet was 1,800 mm wide. Now, 1,200 mm is enough - making it a full third slimmer.” This is a crucial factor for end customers when determining placement. The solution also offers significant benefits in terms of product design and innovation. Additionally, there is still plenty of room for future expansions - just like with the larger, conventional cabinet. Another advantage of the slim design: The transport volume is significantly smaller because eliminating the bulky air conditioning unit also reduces the cabinet’s depth. This not only lowers logistics costs but also cuts the weight from 520 kg to 320 kg.
Control Cabinets Put to the Test
The test series was conducted by Till Jagusch from BEUMER’s Electrical Engineering department. As part of his technical training, he and his colleagues spent six months working on this project for their final thesis.
The focus was on identifying where and how hotspots form - with and without an air conditioning unit. To increase the cabinet’s internal temperature, the BEUMER stretch hood® packaging machine was put under load. Normally, this machine stretches a film over a loaded pallet. To avoid having to remove the film after each measurement, the team cleverly simulated the film-stretching force using strong rubber bands, ensuring the load matched real-world operating conditions.
To heat the surrounding air to 30, 35, and 40°C, the team built a large wooden box as a climate chamber, which was placed over the test cabinets. Measurements were first taken on the conventional control cabinet - both with and without an air conditioning unit - at all three temperature levels. The same tests were then conducted on the smaller cabinet with the AirSTREAM frame, once with an AirBLOWER fan for internal air circulation and once without. A total of 12 test series were carried out, with nine temperature sensors placed inside the control cabinet for each. Additionally, a thermal imaging camera was used to detect hotspots.
Keeping Hotspots Cool
The key takeaway from the meticulously documented test series: With AirSTREAM, the temperature inside the control cabinet is significantly more uniform, preventing hotspots. One example from the 12 measurements: Even at an ambient temperature of up to 35°C, the control cabinet - despite its smaller volume - can still dissipate enough warm air through its outer walls without needing an air conditioning unit.
The compact design of the AirSTREAM frame also provides advantages during cabinet production at BEUMER. Displays and control elements can be more cost-effectively placed in the side wall, allowing for pre-assembly, partial installation, and final configuration according to customer preference - left or right. This flexibility makes installation on the machine easier. A bonus for customers: Wiring the field connections is now much simpler since the terminal blocks are optimally positioned. For an experienced electrical engineer, Hilgenstock calls it “a true pleasure” - every field cable can be connected quickly and effortlessly, with no trial and error required.
Authors:
Rudolf Killmann, Sales Engineer, Friedrich Lütze GmbH
Bernd Hütter, Product Market Manager, Friedrich Lütze GmbH