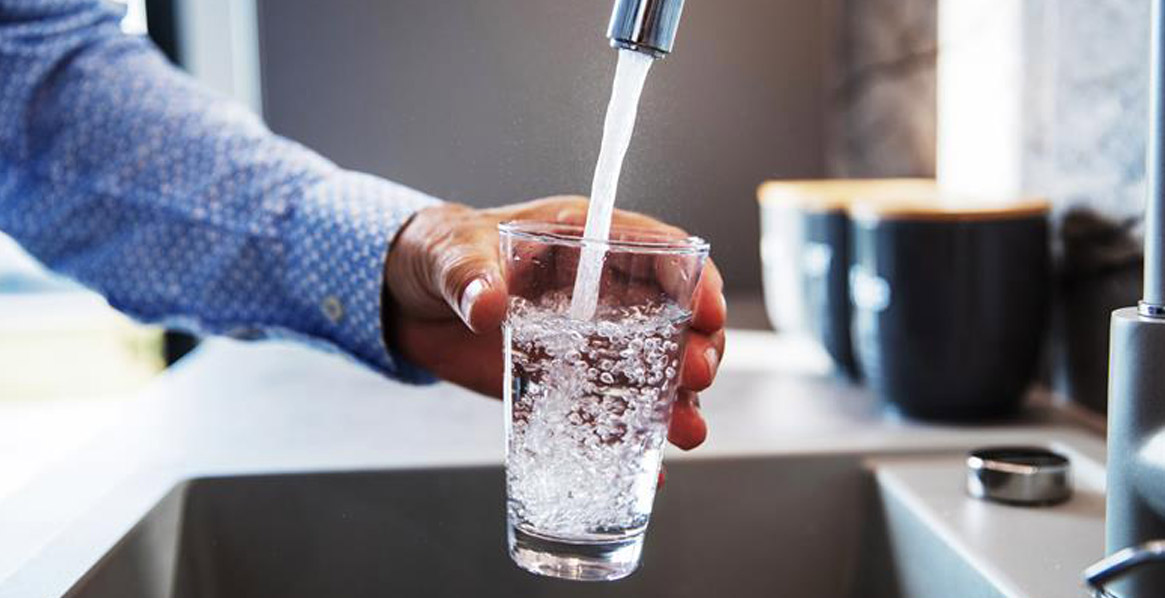
The future of water supply lies in the control cabinet
- Product range:
- Cabinet
Turn on the tap in the sixth-largest city in Schleswig-Holstein, and out flows the “Elmshorn Pipe Pearl.” That is the poetic name the local utility company gives their water. It is drawn from 17 wells, reaching depths of up to 160 meters, and treated at two waterworks to supply 60,000 residents in and around Elmshorn.
To guarantee reliable operation in the future, the utility company modernized its automation hardware. The project was headed by the Elkomp Group, specialists in automation technology and control cabinet construction, who have plenty of experience in delivering highly specialized solutions.
Pilot project for the whole of Germany
Elmshorn needed a complete concept - one that would link decentralized wells, control rooms, and pump management, as well as plant data collection and alarm systems. It also had to guarantee a secure supply under all conditions. That is how the “Waterworks of the Future” came about: a model that other utilities can visit, learn from, and adapt.
The idea: waterworks and wells are operated and monitored via computer systems, based on real-time data. All wells are networked through a server located at the main utility site. Under normal conditions, the new Siemens control system connects each waterworks to its wells over existing lines using an ADSL modem. If communication with a well fails, an M2M connection via the mobile network automatically kicks in, sending fault and error messages. Remote access remains available, enabling remote maintenance. Communication is secured by firewalls and a VPN within this system’s dual-redundancy design. For additional safety, even if the automated control fails, there is a manual control panel on-site to keep the well pumps running if needed. Local access to the wells is protected by an RFID-coded control system that disconnects the control network in case of sabotage attempts.
Control cabinet construction with a future
The “Waterworks of the Future” is now up and running, fitted with cutting-edge products from top automation manufacturers - all neatly installed on AirSTREAM wiring frames.
Elkomp brought in LÜTZE as experts to handle the cabinet interiors. This was a conscious decision by the team: no more mounting plates in the new cabinets. And not just because the space-saving AirSTREAM system cuts down the number of cabinets needed by 30 per cent. “LÜTZE is part of the team because we are building a future-proof concept. Modern control cabinet construction means no more screwing wiring ducts onto metal plates,” explains Sven Drückhammer, Technical Manager at Elkomp. The result is a modular system that fits every control cabinet. “AirSTREAM is extremely flexible, it can grow with the plant and be easily adapted without major rebuilding.”
Smooth water flow thanks to the right control cabinet climate
Another key factor for the lead planner: “High reliability is absolutely vital - but temperature always puts stress on a control system. That’s where the AirSTREAM system, with its innovative thermal management concept, comes in. Hagen Lennartz, Sales Engineer at LÜTZE, adds: “Since AirSTREAM doesn’t use cable ducts, air can flow freely around the components. This creates a uniform climate inside the cabinet - and extends
Author: Hagen Lennartz, sales engineer, Friedrich Lütze GmbH