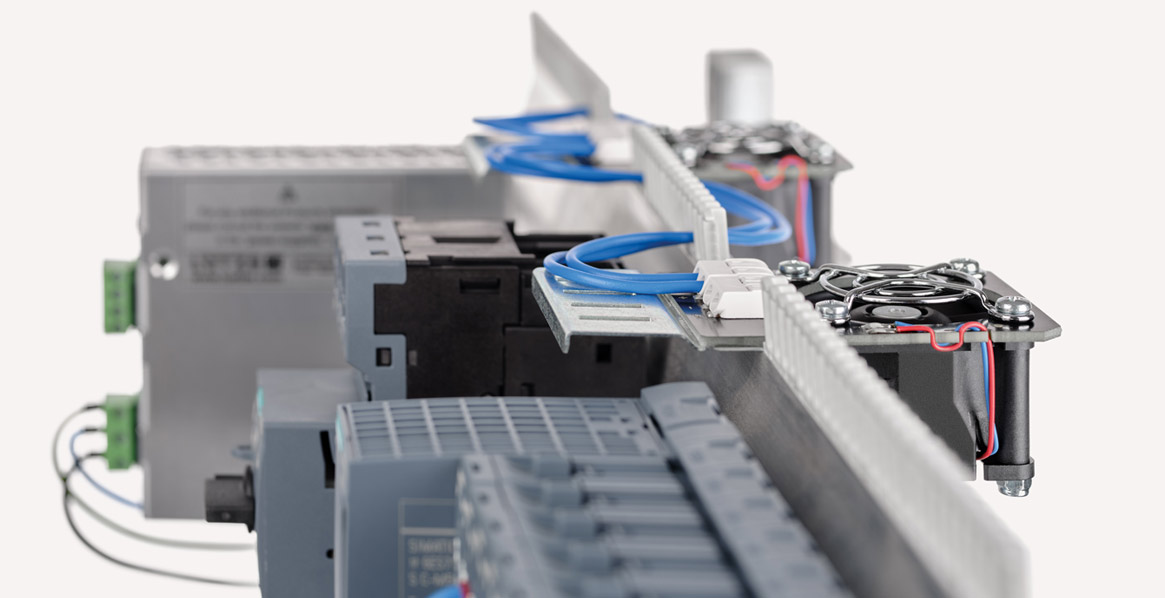
A perfect climate in the control cabinet
Demand-driven control cabinet cooling has become established in many industrial facilities. Intelligent fan systems like LÜTZE AirBLOWER play a central role in this.
LÜTZE AirSTREAM - Pioneering Thermal Concept for the Control Cabinet
Power electronics have been getting smaller and more efficient for many years, allowing more components to be installed in tighter spaces within control cabinets. However, because the thermal loss dissipation is not reduced to the same extent, the heat generated in the control cabinet grows steadily. There is also a greater problem with so-called 'hotspots'.
Once a thermal threshold1 is reached, the heat generated during operation must be actively cooled to achieve a desired average internal cabinet temperature. However, in practice, hotspots can still form around components with high specific power dissipation, even with an installed and correctly sized cooling device, if they are placed in dead zones, for example.
In the early 2010s, LÜTZE introduced a solution with the AirSTREAM wiring frames and the associated thermal concept, where airflow within the control cabinet is actively and intelligently influenced. This means that, in contrast to conventional cabinet constructions, no cable ducts unfavourable for air flow are used. By separating into an assembly and a wiring level, a "chimney effect" is created behind the wiring frame: warm air is removed, depending on the cooling method. Ideally, the cold air is guided downwards to the rear and then to the front and upwards again.
LÜTZE has been offering another wiring frame called AirSTREAM Compact for several years, which possesses the same positive characteristics as the classic AirSTREAM wiring frame but is particularly suitable for smaller control cabinets and junction boxes.
Using air baffles, sub-flows of cold air can be conducted from the back to the front in thermally critical component interstices to avoid hotspots. AirBLOWER fans are used to unify the air layers within the control cabinet and further improve heat dissipation.
This intelligent AirSTREAM concept, as numerous scientific studies have shown, reduces heat stress on components. With AirSTREAM, demand-driven control cabinet cooling has been implemented for the first time, precisely tailored to the heat losses of power electronics, cabinet parameters, and environmental conditions.
Demand-Driven Control Cabinet Cooling Pays Off
Demand-driven cooling concepts have gained traction in many industries. The LÜTZE AirSTREAM wiring frames and components are used in various industries, including food, automotive, semiconductor, packaging, machinery, and logistics. The benefits are obvious:
- Greater environmental friendliness. Sustainability and reducing the carbon footprint are common corporate goals, and they can be more efficiently pursued with a demand-driven cooling concept. It's worth noting that less cooling equipment also means less refrigerant usage, reducing greenhouse gas potential and dismantling and recycling efforts.
- Reduced energy consumption. Electricity costs for operating active cooling media can be significantly reduced through demand-driven cooling and the associated smaller cooling media dimensions.
- Higher level of operating safety. More unified climate control and reduced temperature fluctuations prolong the life of components. As a result, maintenance cycles can be extended, and costs related to premature component failure can be reduced.

AirBLOWER fan family
Key components in the AirSTREAM product family are the AirBLOWER and its smaller sibling, the AirBLOWER Compact. While the larger AirBLOWER is primarily used in traditional control cabinets, the AirBLOWER Compact is preferred in smaller control control cabinets and junction boxes. Depending on the housing size and depth, both fan types can be used simultaneously. Both fan types are delivered ready for installation.
The AirBLOWER and AirBLOWER Compact can optimize the already excellent heat dissipation properties of the AirSTREAM wiring system. Air flows can be directed precisely around the AirSTREAM or AirSTREAM Compact wiring frame. The cabinet's interior sides facilitate heat exchange from inside to outside. Thanks to the friction of the air flows, this is much more efficient than free cooling, where the air only rises and accumulates at the top. Additionally, in combination with LÜTZE AirBLADES, hotspots can be directly ventilated and "cooled." In total, a significantly more unified heat distribution is achieved within the control cabinet. Practical tests have shown impressive results: with AirBLOWER and AirBLOWER Compact, the average cabinet temperature can be reduced by up to 10K.
Two, to a maximum of five AirBLOWER Compact fans are controlled using the LCOS-AB-I control unit in conjunction with up to 3 PT100 temperature sensors. Programming is performed via a standard interface I/O link via FDT/DTM. All parameters can be defined freely: from the temperature control through to clock mode. The operating hours meter records all work parameters. Therefore, the cabinet's temperature condition can be continuously monitored and documented for condition monitoring purposes.
AirBLOWER Compact and AirBLOWER Compared
The smaller Compact fans can fully realize their potential when used on the AirSTREAM Compact wiring frame, with its smaller installation depths, in compact housings and junction boxes. The industrial-grade AirBLOWER Compact fans can be installed during the initial setup or retrofitted into existing control cabinet configurations. Mounting the 50 mm wide AirBLOWER Compact fan is a simple process thanks to a patented solution: Firstly, a 50 mm standard comb segment is removed, and then the AirBLOWER Compact Fan is snapped into the recess. AirBLOWER Compact fans are UL and CE certified and have a power consumption of 6.9 watts at 24 V. The Compact fans have a terminal for connecting the input voltage and another for daisy-chaining to the next fan. This allows up to five units to be connected in series. The voltage supply is direct through the circuit board, and the terminals are easily accessible from the front.
The larger AirBLOWER fan module is installed in the top third of the control cabinet thereby allowing maximum circulation inside the control cabinet. LÜTZE delivers the 24 V AirBLOWER fan modules in a hanging variant that can be easily implemented from the front.
Outlook
Every control cabinet is unique. Therefore, an individual assessment, especially of control cabinet combinations, is essential. The LÜTZE AirSTREAM team advises customers individually on customized cooling solutions. Many factors are considered, such as the type of control cabinet, environmental conditions, which AirSTREAM wiring system should be used, how component placement can be optimized, and how the cooling concept, including AirBLOWER fan modules, can be designed sustainably. Furthermore, LÜTZE offers the possibility of on-site assessments at the customer's location, using measurements to assess the current state and support optimization for a better cooling concept.
For several years now, every control cabinet intended for the market has to be theoretically examined beforehand. This is prescribed by the EN 61439 standard and must be documented. To facilitate this, LÜTZE has developed the online tool AirTEMP, which considers a wide range of practical parameters. With the AirTEMP heat analysis tool, thermal problems and overheated components due to wiring type, device distribution and arrangement, as well as cooling method, can be simulated realistically. These described issues can thus be identified during the planning phase. The AirTEMP configurator is free to use and available to all control cabinet builders and planners at https://airtemp.luetze.com/.
LÜTZE also promotes ongoing collaboration with the scientific community. In cooperation with the Institute for Building Energy, Thermotechnology, and Energy Storage (IGTE) at the University of Stuttgart, LÜTZE has been engaged in the study of thermodynamics in control cabinets since 2011.
1 This threshold value is an individually determinable characteristic for each control cabinet and depends, in particular, on the target indoor temperature itself, the maximum expected ambient temperature, and the spatial dimensions of the control cabinet.
Author: Michael Bautz, Product Manager Cabinet, Friedrich Lütze GmbH